At first glance, the current chip shortages affecting the automotive industry may be considered a completely isolated event: the knock-on effect of the Covid-19 pandemic, which has led to a projected slowdown and untimely supply of orders in early 2020. But it was quickly accompanied by a sudden return of car demand. In this article from Act Group, we will examine the automotive semiconductor supply as well as supply problems in the automotive industry markets and new solutions in this regard.
But a more critical look at supply pressures in recent months suggests a more serious clash of different industry cultures, which is likely to result in continued operational challenges as semiconductors play a central role in automotive electronics and other industrial products.
With the stoppage of the activities of car manufacturers and other industries due to the shortage of microchips, the necessity of fundamental revision in the resilience of the supply chain and business continuity has become inevitable.
This article examines the growing importance of semiconductors in the automotive industry, the culture clash and resulting tensions in the automotive supply chain and automakers, lessons learned, and strategies for optimizing semiconductor supply in the future.
An overview of Zero to One Hundred Exobytes
The automotive industry is rapidly digitizing production lines, and electronic systems have taken over almost every aspect of a modern car.
This trend has been accelerated by the increase in the use of electric vehicles, the use of infotainment systems and autonomous driving. So that it has brought a fundamental change in the automobile industry.
The move to electric cars is not a passing fad. According to the forecast of IHS Markit, the growth of the use of electric vehicles in 2021 will reach 18% compared to the previous year, and this trend will continue until 2026 with a stable annual growth of 7%.
Currently, chip consumption in the entire global automotive sector has reached a level comparable to that of Apple, and each accounted for 8-9% of the $450 billion semiconductor industry market in 2020.
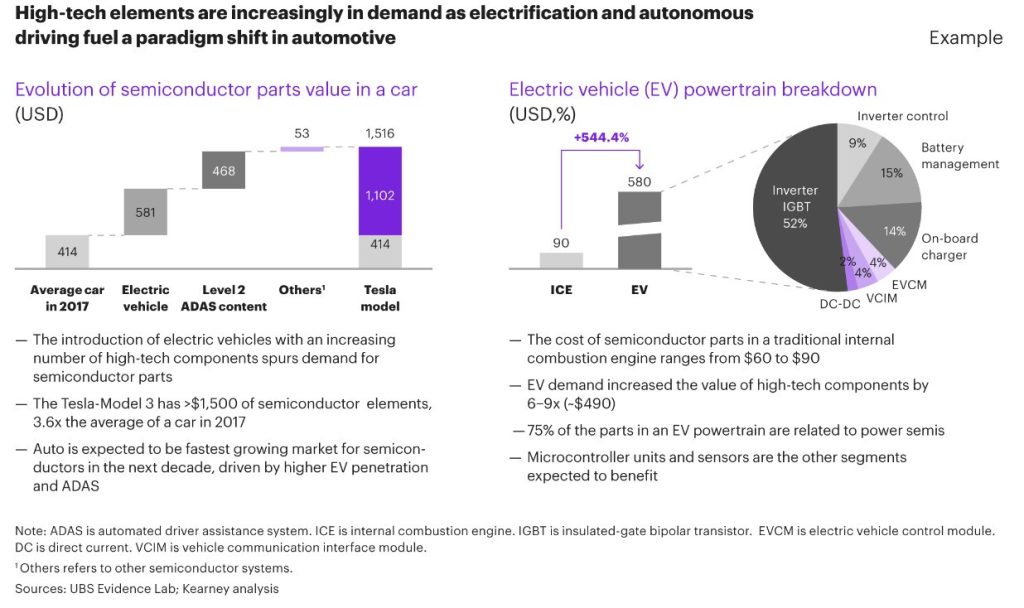
The semiconductor sector in the automotive industry will experience the fastest growth in the next decade, led by the development of electric vehicles and the widespread use of automatic driver assistance systems (ADAS).
But this growth is less compared to electrical appliances, communications, computers and industrial demand.
Meanwhile, tier 1 and tier 2 automakers and suppliers will find themselves in tough competition for critical parts that face capacity and supply constraints in the short to medium term.
Now, the key question in this increasingly zero-sum environment, in which one party will win, is who will need the other party more?
Lack of microchips and supply dependence
When automakers decided to cut production forecasts at the start of the Covid-19 pandemic, their tier 1, 2 and 3 suppliers responded by cutting chip orders to foundries. As a result, many of these foundries, including the Taiwanese company (TSMC), quickly allocated capacity, inventory, and work-in-progress to more profitable, higher-capacity customers.
Due to the limited foresight of car manufacturers, the supply of more than six months was directed to other industries, and semiconductor or microchip production factories left a limited space to change production and accept new orders.
Supply bottlenecks for automotive microcontrollers (MCUs) and central processing units (CPUs) extended delivery times from 16 to 26 weeks, pushing delivery back to the fourth quarter of 2020.
As a result, major automotive chip designers such as NXP, Renesas, and IFX, which had outsourced manufacturing to TSMC or, in some cases, SMIC in China, were left with few viable options.
Beyond MCUs and CPUs, supply segmentation and the automotive sector’s reliance on older technology _200mm wafers, with sensors operating at 10-180nm nodes_ has exacerbated automotive semiconductor supply.
According to IHS Institute, the total revenue of the automotive industry in the semiconductor sector will reach about 44 billion dollars in 2021, in which the evolving combination of the growing segments of self-driving cars and electric vehicles will play a central role.
However, it is unlikely that the car’s share of the total market will change much compared to other competitors.
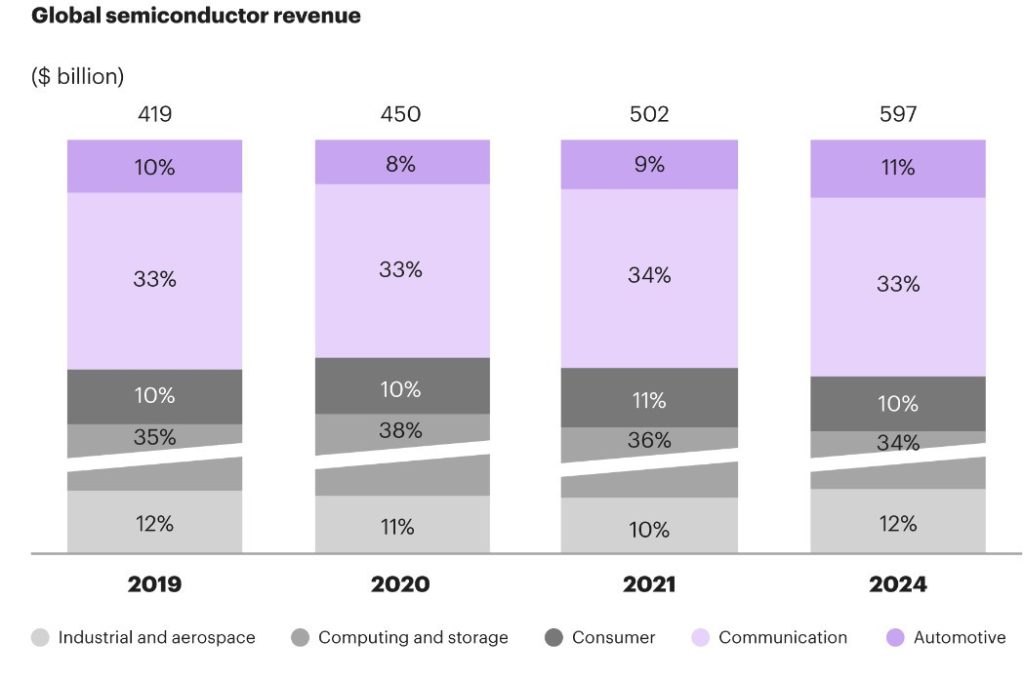
As the future moves toward more advanced technologies (eg, sub-10nm nodes and 300mm wafers), inter-industry competition for supply is also likely to remain.
This in turn prompts a broader conversation about supply dependence and scarcity against the backdrop of industry culture and supplier-buyer dynamics.
New thinking solutions for semiconductor supply
Three key features of the automotive industry will be effective in framing the supply challenges:
The automotive industry is hierarchical in performance and cost management, with a strong top-down focus.
Automotive manufacturing relies on continuous flow and just-in-time delivery (JIT) and lean manufacturing. Inventory is minimal, often monitored hourly. A potential disruption could shut down lines or entire plants.
The automotive industry’s demand for semiconductors from chipmakers is a diverse mix characterized by fast growth, but a reliance on older, less valuable technology in a market of increasing automotive complexity and uncertain sales.
Given the unique market position for microchip supply compared to the more traditional commodities they are more accustomed to, automotive companies can consider a range of approaches in rethinking semiconductor supply strategies and networks.
They should develop a different and more collaborative relationship with microchip manufacturers, with better demand forecasting and information sharing.
From our point of view, among the most promising solutions, forming a multi-company decision-making room, reviewing the supply model and establishing a common supply chain are considered.
Alone or in combination, these solutions must all be considered within the context of a broader strategic vision and set of goals.
Automakers and partners on a common page
The dual mission of ensuring inventory and allocating supply to production priorities that actually bring the most profit can be achieved with proper coordination between supply chain partners.
In a multi-firm structure, automotive players can bring together Tier 1 and Tier 2 suppliers and seek to aggregate and coordinate demand into a single, expanded “channel.”
This decision room works on the question of how to ensure the precautionary inventory of the manufacturing process along the entire value chain-from the Tier 2 supplier to the manageable inventory of wafers of key semiconductor suppliers.
While today the level of broad/multi-company supply coordination between automakers and semiconductors is limited compared to the high-tech sector, cases such as Tesla/Broadcom/TSMC and more recently Conti & Bosch/Recogni are examples of this potential.
Reset provision for business continuity and purchasing power
JIT inventory management and cost management have played a key role in automotive semiconductor supply.
While the semiconductor value chain is characterized by lead times of six months or more, with limited short-term flexibility to adjust production.
The automotive industry must align its supply chain and procurement practices with the semiconductor industry to stay in business.
Demand planning can become more agile to generate faster demand signals at all levels of the value chain.
Active collaboration with manufacturing plants, including broader supplier follow-up and relationship management, can help build a shared vision of planning requirements and purchasing commitments.
consider forming a global purchasing alliance consisting of several automakers and their suppliers, supported by a transparent product-in-process (WIP) and inventory allocation mechanism.
This alliance can take on a similar procurement role with major manufacturers such as Foxconn in the consumer electronics and high-tech sector, leveraging the collective purchasing power of the industry as well as ensuring supplier development and readiness.
The alliance can also maintain minimum inventory and supply, enter into competitive pricing flows, manage shared inventory, activate existing parts of the automotive supply chain, and even maintain purchasing capacity to manage peak demand.
Promoting collaboration for risk
management
Most of the players in the automotive industry and their subsidiaries have very little spare inventory.
Relying on the extended multi-firm concept, automotive companies can rethink their supply chain strategy and key performance indicators (KPIs) with a view to creating strategic buffers, inventory and product in the manufacturing process (WIP) at multiple reinforcement points in the network.
More direct control over the semiconductor supply chain is achieved in a variety of ways.
An interesting example of an automaker that has outperformed during chip shortages is BMW, which learned from semiconductor shortages in 2011 and moved early on to a more direct relationship with chip suppliers.
Japanese companies such as Toyota have benefited from strong relationships with suppliers through the traditional Keiretsu system, which provides greater control and transparency.
By opening up their definition of “critical” ICs , automakers can gain more transparency in the range of suppliers and the place of components in the value chain.
They can share this information with their supply chain teams while providing advanced supply risk tools for real-time monitoring in a set of easy-to-understand measures.
Risk profiles for this class of components should consider the total value at risk and align with doctrines, policies, and mitigation measures for specific suppliers or semiconductors/circuits required in the future.
The future will be completely different
With the view that the current semiconductor shortage is indicative of a larger dynamic, it is reasonable to expect that many of the forces in automotive semiconductors will apply to companies and independent manufacturers alike entering the digital world.
As companies redefine their semiconductor supply chain landscape to match evolving needs, they must rethink much of their current operations, from engineering practices to digital enablement, supply chain management to supplier relationships.
They must recognize that their core business capability is inherently inter-industry or joint competition for critical components, and regardless of relative size or past legacy, they must take steps to work more closely and proactively with a supplier base that is both It surpasses and disrupts many old industries.
All in all, automotive companies need to make their core capability more like a high-tech company. Success in facing this challenge requires fresh thinking and a bit of hard work, and will largely depend on culture and competition.
0 Comments