The automotive industry, which is in the list of driving industries of every country, has been facing a challenge called electric cars for nearly three decades. The idea of producing an electric car seemed very attractive for the nineties when internal combustion cars had created high noise pollution and a high share of air pollution was attributed to them. We must add that in those days, the horror of the oil crises of the 80s was still present in the minds of industrial policy makers. But with all these interpretations, the market share of electric cars compared to internal combustion cars is still less than 3%, and in total, car manufacturers were able to sell about 8 million electric cars in 2018. In this article, act group only wants to have a look at the Application of polymers in electric vehicles.
Electric vehicle (EV) is a car that uses rechargeable batteries as an energy source and an electric motor as a driving force.
The batteries used in these cars are rechargeable lithium-ion batteries that feed the engine. In many cases, the electric car is similar to the gasoline and diesel car, and the only difference is the replacement of the combustion engine with a rechargeable battery. This battery supplies the electric motor and the electric motor drives the wheels.
Electric cars are becoming more and more popular because they are emission-free and do not produce carbon dioxide or particulate matter.
These pollutants are effective in global warming and damage to air quality, especially in urban environments.
Figure 1 shows the overview of the electric car along with the location of the battery in these cars.
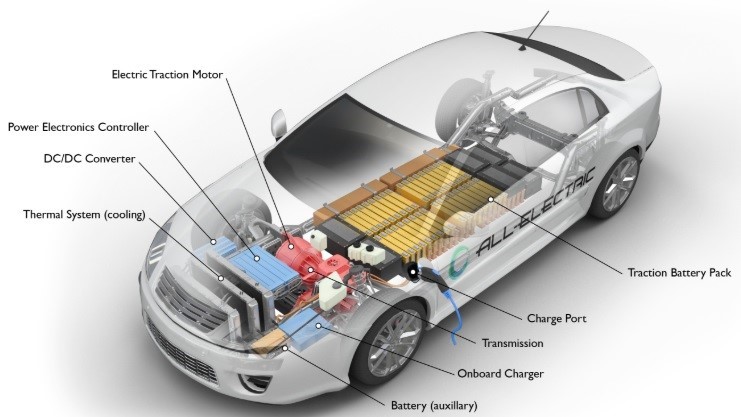
Figure 1: Overview of battery location in electric vehicles
Market share of polymers in electric vehicles
According to the latest reports, the global market size of polymers in electric vehicles was 6.91 billion USD in 2020, which is expected to reach 418.27 billion USD in 2028 due to the expansion of electric vehicles.
This increase in the market share of polymers is due to the creation of new opportunities in electric propulsion and the increase in the volume of units.
Increasing the polymer consumption factor has reduced its weight without affecting the performance of the car.
More than 70% of the plastics used in electric cars consist of four main polymers: Polyamide (PA), Polypropylene (PP), Polyurethane (PU) and PVC.
The use of other engineering thermoplastics that have resistance to heat and high electrical currents has also increased in electric vehicles.
Polymers such as polyetheretherketone (PEEK), polytetrafluoroethylene (PTFE), polyethyleneimine (PEI) and polyimide (PI) have shown excellent resistance to heat and heat, so there seems to be little argument for Metals (which are at least two to three times heavier) are used in parts where these polymers can be used.
The move from internal combustion engines to batteries creates new opportunities for polymers. Among other things, the operating temperature is greatly reduced, but flame retardancy is still critical.
Currently, engineering polymers are available with properties such as flame resistance, electrical insulation, thermal conductivity, and cooling system compatibility.
It should be noted that electric vehicles require a different cooling system than internal combustion engines, which may make certain types of vehicle windshields and front facades obsolete, thus creating opportunities for new designs in electric vehicles based on advanced plastics.
The role of polymers in electric vehicle batteries
Electric vehicle charging infrastructure is another important issue where battery components must exhibit excellent mechanical performance at high temperatures and high dimensional stability.
It is necessary for these components to withstand harsh conditions while providing long-term safety and durability for paint, surface finish and UV stability.
In places where electricity flows, connectors and cables will be needed, and the plastics used must exhibit the properties of electrical insulation, flame resistance, and resistance to hydrolysis. An electric vehicle depends on the efficiency of the battery and the use of stored power.
Anything that helps minimize current leakage from the system will help improve battery life and thus the distance that can be traveled on a single charge. Polymers such as PTFE and Polyimides are very effective as insulators in high voltage and high temperature applications.
The use of sensors is essential to ensure safety. As autonomous vehicles gain traction, sensors will likely become the most important component in a vehicle.
Also, polymer shields and connectors are important because, unlike metals, they remain ineffective against the signals and waves sent and received by the sensors and do not cause interference.
PTFE and PEEK are currently widely used as radomes of antennas (antenna cover: a spherical structure made of polymer to protect the antenna from natural factors).
These unique polymers can be resistant to weather and heat, in addition to not interfering with signals in any way.
The proliferation of vehicle battery systems with higher energy density creates a greater need to protect occupants from fire hazards.
Flame-retardant polymers, including adhesives and fabrics, can help reduce the risk of fire spreading.
Also, the battery separator plates based on advanced polymers, which are used in lithium-ion batteries, can guarantee temperature stability and increase the range of use. Both PTFE and PE (polyethylene) polymers are used as battery separators.
The recent increase in the price of polyvinylidene fluoride (PVDF) is almost entirely the result of the amount required of this polymer to produce EV batteries.
It is estimated that each EV battery On average, it requires about 6.5 kg of PVDF, which is used both as an electrode adhesive and as a battery separator coating material.
The role of polymer compounds in electric vehicles
If one day electric cars become widespread all over the world, the business in the world of polymers and polymer compounding industry will also be different.
In general, electric cars need more polymer parts (due to the need to lighten the components of these cars to achieve more navigation) compared to internal combustion cars, and they will also have stricter requirements.
For example, the resistance to the creation of a flame and its spread, and even the temperature resistance of the polymers used in electric cars must be much higher than in internal combustion cars.
(For example, the cooling system of electric cars is active both during servicing and charging) Or in another example, if LFT technology can reduce the weight of the chassis and body of electric cars, the mileage of these cars will increase with each charge.
Since there is a high electric load in the electric circuit of these cars, all external parts, including polymers, must have high electrical resistance.
Also, due to high electric current and high usage temperature, the resistance of colored compounds should be special and not change color.
Figure 2 shows the image of polymer parts produced with colored compounds that have high thermal and electrical resistance.
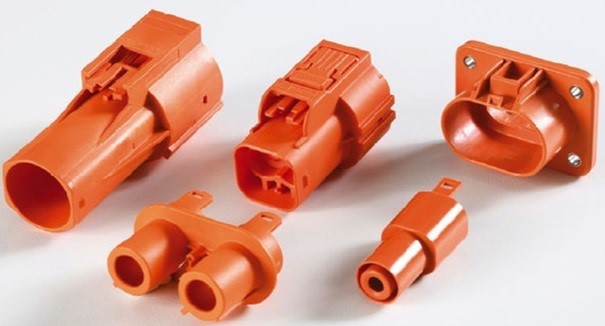
Figure 2: Polymer parts produced with colored compounds in electric vehicles
But if we go to the more specialized compounds used in electric cars, we should talk about the heat conducting engineering compounds.
In the battery and driving forces of these cars, basic compounds of engineering plastics are needed, which are also heat conductors, and these compounds require a special technology for production.
Another group in the category of special polymer compounds are electromagnetic wave absorbing compounds.
In fact, the standards of electric vehicles in the driving force sector require raw materials that can prevent the interference of electromagnetic waves.
Polymers cope well with this important task with the help of special additives.
The role of polymers in the internal and external trim of electric cars
Along with the developments that have occurred and are evolving in the polymer compounding industry specifically for electric vehicles, efforts are underway in the field of polymers used in cabins such as internal combustion vehicles.
In this context, we can mention innovations in the production of seats with modified PU foams in order to increase the safety and comfort of passengers, as well as the luxury production of dashboard components and interior trim.
The use of fillers and reinforcements, as mineral components of polymer parts, has been common since about 100 years ago.
Fillers are added to the formulation of various parts in order to reduce the price and reinforcements to improve the mechanical and thermal properties of polymer parts.
But in recent years, a new technology has been commercialized in the field of strengthening polymers.
In fact, an important group of reinforcements are natural and synthetic fibers such as glass fibers, which in the past were added to polymers in a chopped form in mixing devices to improve distribution and distribution in the polymer matrix, as well as feeding.
But in the technology known as LFT, which stands for Long Fiber Thermoplastic, reinforcing fibers are added to the polymer without crushing and with the help of a special mixing device, and then in the granulation stage, they are cut into larger pieces than normal granules.
The mechanical strength and modulus obtained in this method is much higher than normal fibers.
Different polymers such as PP and PA obtain exemplary mechanical strengths with the help of LFT technology.
It is expected that in the not too distant future, LFTs will replace many metal parts in automotive and industrial applications, or in their current applications, they can greatly reduce the weight of the parts and prevent the production of more greenhouse gases.
Glass fiber is the most important reinforcement used in the production of LFTs. However, other fibers with even higher efficiency, such as carbon fibers, steel, aramid, etc.
Are used in special applications. Figure 3 shows the polymer base parts related to interior trim produced using LFT technology.
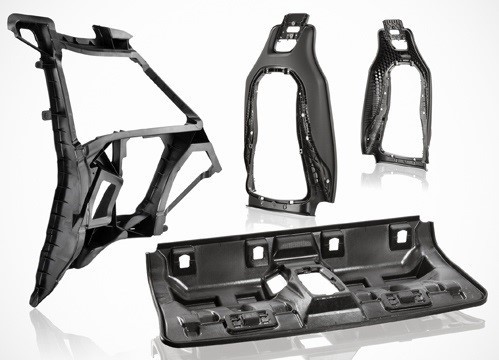
Figure 3: Interior trim parts produced using LFT technology
LFTs are still at the beginning of their development and have found a limited market in the automotive, military and aerospace industries.
If we want to take a closer look, we should say that around 300 million tons of polymers are produced annually in the world’s petrochemical industries.
Of this amount, about 50 million tons are reinforced in compounding units. The share of LFTs in this reinforcement is about 1% and is equal to 490 thousand tons every year.
After PP and PA, two other important polymers used in LFT technology are ABS and PBT. Picture 4 shows car seat frames with the help of LFT technology.
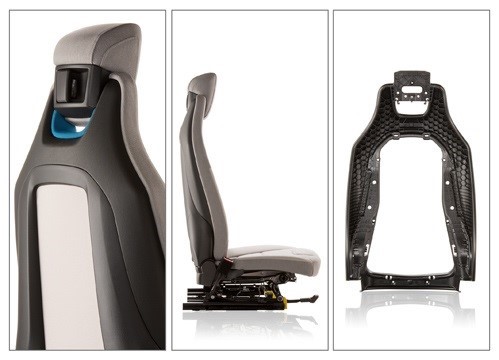
Figure 4: Polymer chair skeleton produced with the help of LFT technology
LFT technology has a lifespan of about 7 years, but so far it can be said that the future of this technology is tied to the development of the automotive industry.
Because at present, almost all applications of LFT- based products have been installed and used in cars.
Among the most important parts that are produced with the help of LFTs, we can mention the door frame, the tray under the engine, the fan and radiator frame, the set of pedals, the battery holder in electric and hybrid cars, the dashboard frame, the frame of the seats, etc.
Currently, Japanese automakers use up to 1 kg and some European automakers up to 6 kg of LFT in the production of parts for each of their cars.
Due to its high performance and the possibility of recycling, LFT can also be placed in the family of green and nature-friendly polymers.
References
- https://futurism.com/the-byte/plastic-car-electric-vehicle-japan/
- https://www.automotiveplastics.com/mobility-trends/electrification/
- https://www.ulprospector.com/knowledge/12939/pe-polymers-for-electric-vehicles-ev/
0 Comments