Overview of Car Crankshaft Production Methods and Factors Affecting its Performance
Published by Baadl on

Crankshaft is considered one of the most vital components in the internal combustion engines of cars and has an impact on the full performance of the engine. This part is involved in the process of creating the rotational movement of pistons and rods, and without its optimal performance, the engine is not expected to work well. In act group, we analyze the production methods of the car crankshaft and the factors affecting its performance.
Considering that the crankshaft faces a large number of load cycles and multiple stresses during its life, the importance of choosing the right materials for its construction becomes more clear. In addition to materials, production methods also play an important role in the quality and performance of the crankshaft.
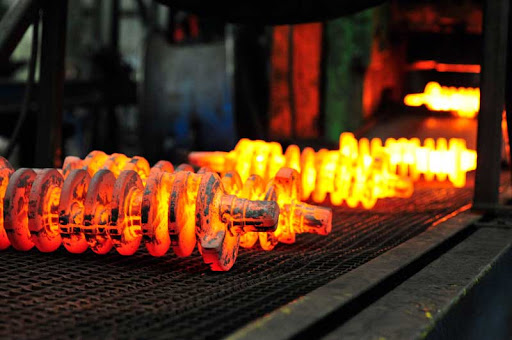
Accurate processes and accuracy are very important in making this part. Crankshaft production using advanced technologies and the correct execution of its manufacturing steps depends on the skill and expertise of production experts and technicians.
In general, the crankshaft as a main and important part in the internal combustion engines of cars is very important not only for the optimal performance of the engine but also for the safety and durability of the car. Therefore, the choice of alloy and production methods of car crankshaft is very important.
Introduction
The crankshaft is a part of the car engine that is driven by a group of pistons. This piece transfers the torque to the gear and this causes the gear to rotate. In addition, the rotation is transmitted on the driving axes. The optimal performance of the engine and the safety and durability of other car parts depend on the performance of the crankshaft.
Production methods of car crankshaft:
Casting:
In the casting method, the crankshaft is formed by melting, pouring the melt into a container called a mold, and then cooling and freezing it. This method is suitable because of its efficiency and ability to create complex shapes.
Blacksmithing:
The forging method is one of the important methods in the production of crankshafts, which is widely used in the automotive and mechanical industries. In this method, metal materials are formed by high pressure and heat to form the final crankshafts.
The forging method is one of the production methods of car crankshaft, which is widely used in the automotive and mechanical industries. This process is mostly used to produce parts with high rotational load tolerance and special requirements.
In this method, the crankshaft is formed from a steel billet in a round shape, and then using CNC machining and other precision processes, the final shape of the crankshaft is obtained. This method is very suitable for producing precision crankshafts.
Choosing the right materials is very important in the manufacture of crankshafts. Austamped cast iron has high tensile strength and excellent mechanical properties and is highly regarded in the production of crankshafts.
Austamper heat treatment creates a special spherical and graphite structure in cast iron, which distinguishes this material from other ordinary cast irons. Austamped cast iron has the ability to withstand high rotational loads and is used as one of the main materials in the production of crankshafts.
In recent years, the use of quench tempered steels with tensile strength, mechanical properties and high toughness has become very common in the manufacture of crankshafts.
High-strength low-alloy steel is called micro-alloy steel, which is prepared by adding a small amount of alloy elements such as vanadium, columbium and titanium. The most important advantage of microalloy steels is the reduction of energy consumption and cost in production, especially in the automotive industry.
In these steels, it is possible to achieve the desired strength and other properties after performing hot work at high temperature and controlling the operation parameters, as well as proper cooling to low temperature. It is comparable. As a result, by eliminating quench and temper operations, in addition to reducing costs, the production speed can also be increased.
In recent years, many efforts have been made to develop a new generation of steels under the name of steels with a bainite structure, which can have certain advantages in the performance of the crankshaft.
Review of sources
Blacksmithing:
As mentioned, quench tempered steels are one of the most widely used alloys in the production of crankshafts by forging method. These types of steels are used in the manufacture of crankshafts due to their good mechanical properties and fatigue resistance.
One of the ways to improve the properties of quench tempered steels is to add alloying elements. Siti et al showed that the addition of molybdenum to quench tempered steels increases fatigue and leads to improved wear resistance.
If high carbon steel is used, by heating the part to austenitic temperature (on the surface) and then quenching, the surface will turn into martensite. In this method, due to incomplete austenitization below A 1 temperature , a soft layer may be created under the boundary of the hard zone.
Microalloy steels are another type of steels used in the production of car crankshafts. Like quench tempered steels, the mechanical properties of microalloyed steels can be improved by adding some alloying elements.
Siti et al showed that by adding 3.42% titanium to microalloy steels, grain growth can be controlled and mechanical properties can be improved.
Also, their results showed that by dissolving vanadium in the austenite phase, the percentage of carbon can be kept low, and in this way, the strength and welding capability can be improved, and the temperature required to perform the forging process can also be lowered. Niobium can be mentioned among other alloy elements that improve the strength of microalloyed steels.
One of the common defects and problems in forging parts is decarburization of the surface. To solve this problem, we need to use rapid heating up to 1000 degrees Celsius in hot forging. Although the use of cold forging leads to higher dimensional accuracy, on the other hand, it also reduces the life of the piece.
By reducing friction, the use of phosphate coating reduces the force required for forging and increases the life of the mold. In Table No. 1, the process of forging the spindle is summarized.
pic
Adding chromium and molybdenum elements to steel makes the crankshaft core cool with a suitable cooling rate and the part is completely hardened. Also, to improve machinability, 0.1% lead or sulfur is added to steels.
By comparing the fatigue properties of microalloyed steels (0.06%-0.08% V) with quench tempered steels (SAE 1050) and SAE 4140, they found that microalloyed steels have fatigue properties comparable to quenched tempered steels. Also, in the 3-year production scale, microalloy steels showed economic savings of 9-11% compared to quench tempered steels.
Casting:
One of the common methods in the production of crankshafts is the casting method. The materials used in casting play an essential role in the properties of the final piece. Christian et al showed that the fatigue strength of austempered cast iron is twice that of pearlitic cast iron.
Also, the use of stamped cast iron saves 30% compared to steel forging. On the other hand, Walbot showed that cast iron with a spheroidal graphite structure has higher strength (95,000 PSI vs. 80,000 PSI) compared to gray cast iron used in the production of crankshafts.
By comparing 1045 or 1053 forged crankshafts, Walbot noticed that the elongation of forged crankshafts is higher than that of cast ones. Walbot showed that turning from a billet, forging, and casting are of better quality, respectively, for making crankshafts.
Cranks machined from a billet have a strength of about 165,000 PSI, but because-turning is an expensive process, forged cranks are preferred. Forged crankshafts are made from chrome-plated 5140 steel with a strength of 115,000 PSI, and 4340 steel with a strength of around 145,000 PSI.
Methods of improving crankshaft fatigue properties
Nitrating
Siti et al showed that surface nitriding improves fatigue properties. However, by comparing 23 MnCrMo 5 and 42 CrMo 4 quench tempered steels with 25 MnCrSiVB 6 quenched steels, they showed that 25 MnCrSiVB 6 quenched steels are more easily nitrated and the depth of the nitrated layer is greater in them.
For nitrating, the piece must be placed in an atmosphere containing NH 3 at a temperature of about 500-520 degrees Celsius, so that hard compounds such as Fe 4 N and Fe 3 N are formed on the surface of the piece, which cause the expansion of the iron network and increase the hardness and strength.
It leads to fatigue. Like quench tempered steels that use nitriding to increase surface hardness, microalloyed steels also use heat hardening to increase surface hardness. In this way, a compact layer is formed on the surface, which prevents the formation and growth of cracks and improves the fatigue properties.
It should be noted that nitriding is used only for certain parts due to low productivity, but on the other hand, nitrocarburization is used for most parts.
For carbonization of steels, which improves fatigue properties and wear resistance, the concentration of carbon in the atmosphere must reach 0.8%, and after carbonization, the part is quenched until it reaches the martensite structure.
Fillet roll
One of the processes that is used to improve the fatigue properties and increase the resistance to failure in metal parts is felt rolling. This process is done specifically on the edges and corners of the parts and has a great effect on increasing the durability and strength of the parts.
Swick et al showed that local plastic deformation creates compressive residual stresses in the rolled fillet regions that compensate for service-induced tensile stresses and delay crack initiation and growth. Therefore, the fatigue strength for unrolled felt crankshafts is 201 MPa and for rolled felts is 811 MPa.
Also, Swick et al observed that the fatigue cracks are located above the central part of the rolled felt areas. This is due to the concentration of tension in this area.
Summary of the research done
Table 2: shows a summary of the research done on the car crankshaft part
Table
Summary
In the above article, various production methods of car crankshaft, including forging, casting and turning, were examined. Each of these methods has its advantages and disadvantages. Forging provides strength, stability and high dimensional accuracy.
In recent years, microalloyed steels have been used to produce crankshafts with the help of forging. Although the complexity of the process and the limitation in the production of complex shapes can be seen as negative points of this process.
The casting method has a higher production speed and also the possibility of producing more complex shapes. At present, the most interesting material for producing cranks in this way is austempered cast iron, which offers good mechanical properties.
However, secondary costs such as heat treatment and machining may be challenging. Turning is known as a precision method that gives designers the ability to offer more diverse designs regardless of process limitations, but it may involve high cost, time, and material wastage.
Finally, choosing the right method for crank production should be done according to the needs and specifications of the design and the final product.
0 Comments