Ceramic matrix composites are a subgroup of composite materials that include fibers embedded in a ceramic matrix. The field and fibers include any type of ceramic material, due to which carbon and carbon fibers are also considered as a ceramic material. In this section, we describe ceramic composites in car parts in detail for you in Act Group.
The driving force behind the development of ceramic composites has been to solve the problems related to conventional technical ceramics such as alumina, silicon carbide, aluminum nitride, silicon nitride or zirconia, because these ceramics are easily subjected to mechanical and thermomechanical loads due to cracks caused by micro-defects or abrasives.
They are separated from each other. Crack resistance like glass is very low. In order to increase crack resistance or fracture toughness, particles of single crystal whiskers are embedded inside the matrix.
However, the improvement of strength is limited and the manufactured products are mostly used in the field of cutting tools. So far, only the integrity of long multifilament fibers1 has greatly increased the resistance to cracking, resistance to elongation2 and thermal shock in several new applications.
Among the commercially available ceramic composites, C/C, C/SiC, SiC/SiC and Al2O3/Al2O3 can be mentioned, which differ from traditional ceramics in the mentioned properties, which are mentioned below:
- Elongation to failure up to 1%
- Great increase in fracture toughness
- Strong increase in shock resistance
- Improving the ability of dynamic loading
- Non-isotropic properties according to fiber orientation
Read More : Explore Top Auto Parts Store Businesses in Iran
Comparison of ceramic and metal composites
- The ground phase of the composite is a metal ground, not a polymer or ceramic, but a pure metal or metal alloy.
- Metal base composites from ceramics or ceramic base composites (CMC has more flexibility and toughness). Compared to unreinforced alloys used in the field, these composites have less flexibility and are weaker in terms of toughness.
- The role of reinforcement in metal-based composites, similar to polymer-based composites, is to increase strength and elastic modulus, but in the case of ceramic-based composites, the reinforcement is more responsible for reducing damage caused by warping.
- Metal-based composites generally have a larger heat capacity than polymers and polymer-based composites, but their heat capacity is lower than ceramics and ceramic-based composites.
CMC composites in car parts
Ceramic brake and clutch disc
GT3 super sports cars They are the first standard devices produced in the world in which ceramic composite clutches are used (Figure 1).
The dual disc dry clutch developed by Porsche meets all the requirements in terms of combining a smaller diameter and low weight with a long service life.
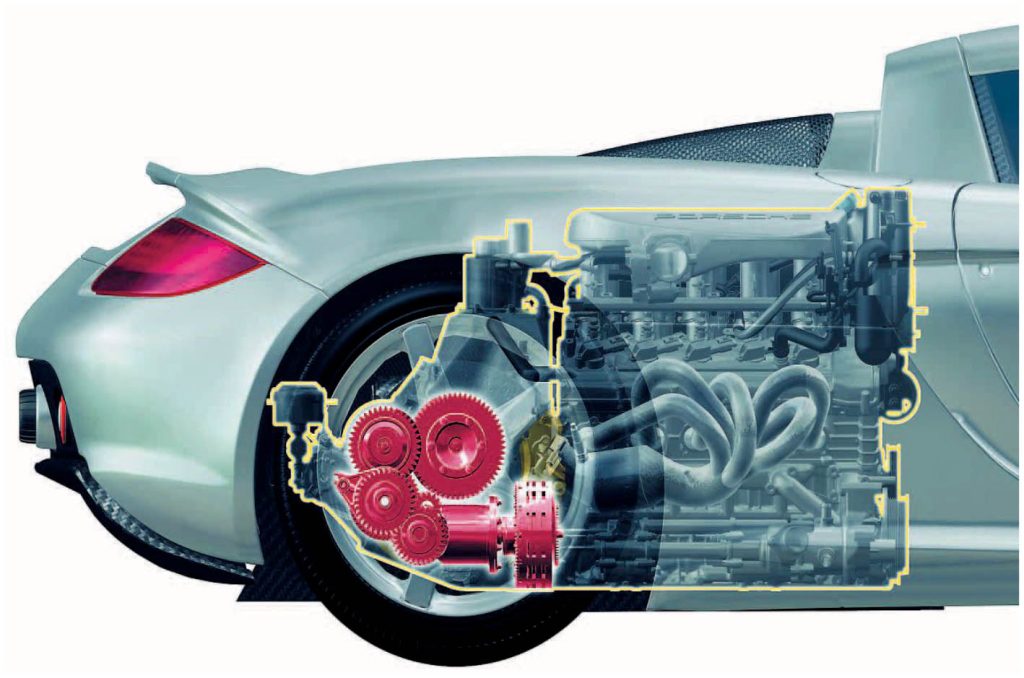
Figure 1: Using a ceramic clutch lowers the center of gravity for the engine
The general vision for building a super sports car is to model the idea of existing racing cars that are suitable for everyday use while still being able to be built on a small scale.
One of the main topics here is the clutch system, which needs to be lightened and reduced in diameter as much as possible, because the position of the center of gravity is a critical factor in a super sports car.
The smaller the clutch and the distance between the crankshaft bearings 4 And the lower part of the engine compartment is shorter, the engine is placed lower and lowers the center of gravity. In the past, only a carbon fiber clutch was able to provide this racing specification.
However, this characteristic is involved in requirements such as lifetime service, driver comfort and practicality in everyday use.
Since there was no suitable clutch system on the market for the Carrera GT, Porsche engineers teamed up with a select few colleagues to develop a completely new clutch using innovative materials used in the friction discs and linings (Figure 2).
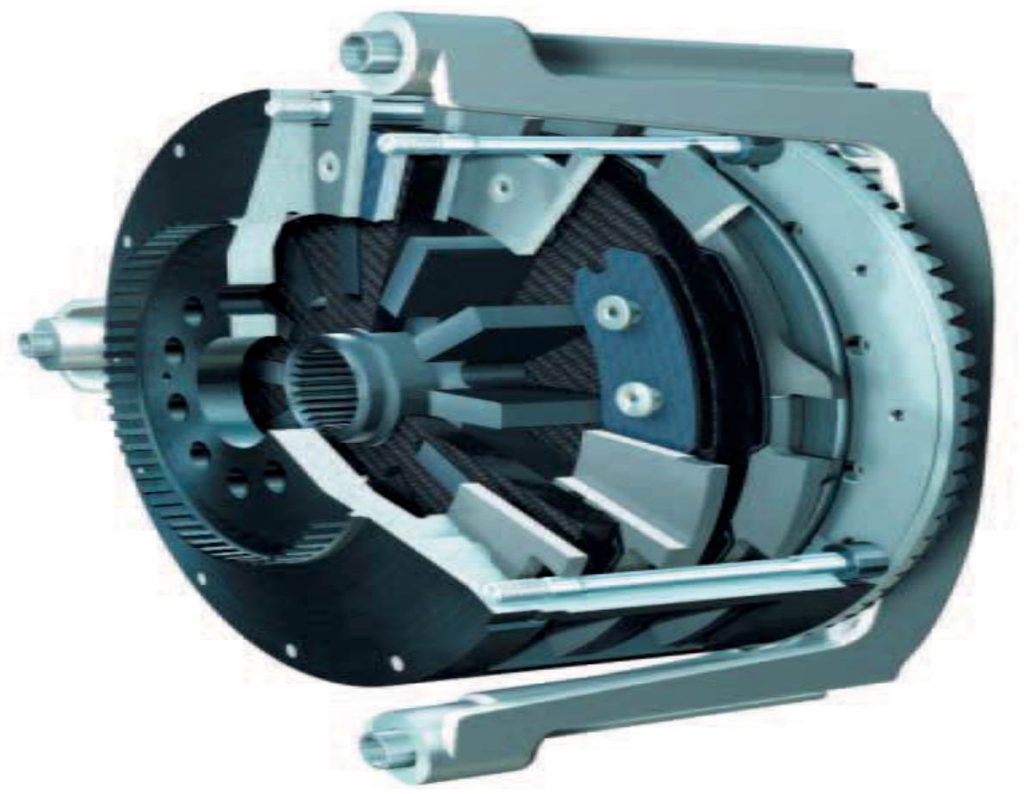
Figure 2: The Carrera GT is the first standard vehicle in the world to use the new ceramic clutch
Continuing these efforts, the specialists were able to obtain 5 PCCBs (Porsche Ceramic Composite Brakes).
The brake reinforced with ceramic materials in the form of short fibers 6 has proven an excellent feature such as high strength, good heat resistance and high durability.
In the first test, the conventional clutch was configured with a short ceramic fiber. This material could not withstand the tension created by the centrifugal force.
By using a structure including carbon fibers as the load-bearing part 7, the strength of the silicon carbide discs reinforced with carbon fibers has been increased to such an extent that the clutch system is able to withstand speeds above 20,000 rpm with extreme thermal load without causing any damage.
Several layers of carbon fiber fabric are processed with carbon-rich resin to produce a sheet-like material that can be carbonized at approximately 800°C and siliconized at 1400°C. Single-cut discs are produced from ceramic plates using a water jet cutting tool (Figure 3).
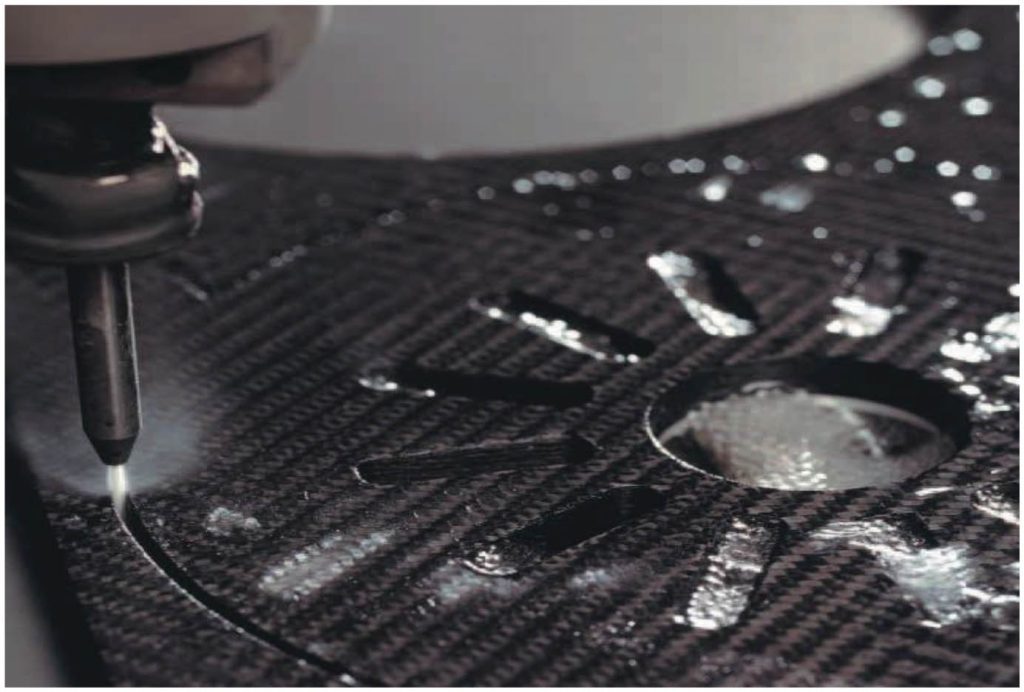
Figure 3: Water jet under 3000 bar pressure separates the friction disc from the ceramic plate.
Subsequent tests confirm that these discs are now able to overcome high amounts of stress and exhibit wear at a very slow rate (Figure 4).
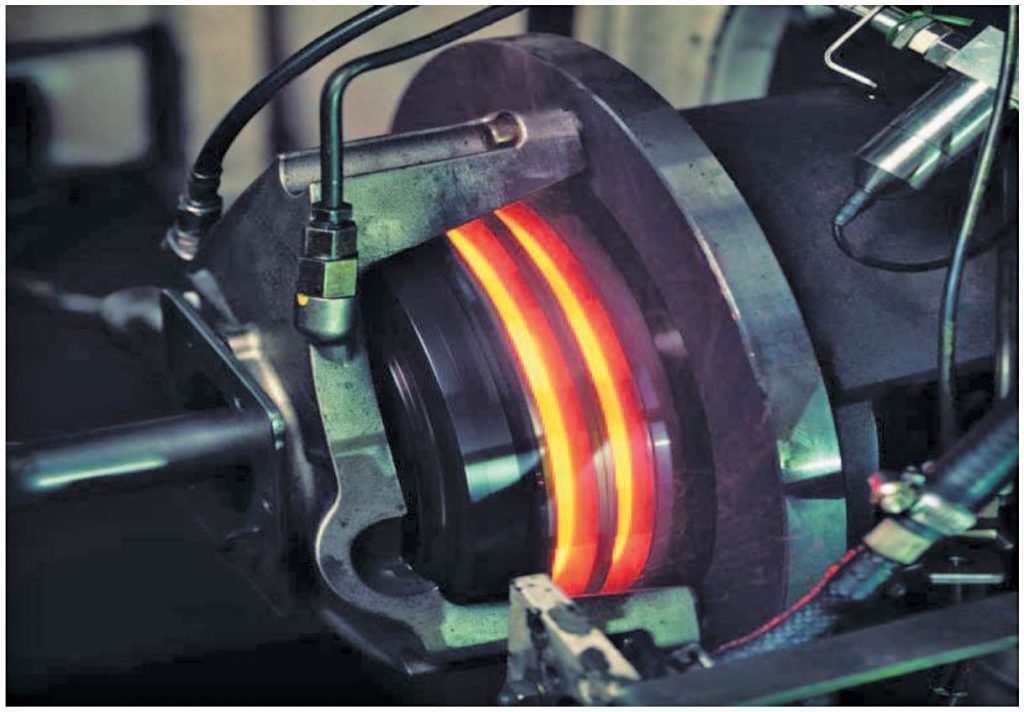
Figure 4: Ceramic composite clutch in overload test on Porsche test bench
The comfort of the driver is also considered so that this dynamic 10-cylinder engine with extremely low rotational mass created a special challenge for Porsche developers to create a smooth and comfortable movement.
Synchronization of manual transmission due to the need for variable forces 8 The bottom was optimized.
When the tests were carried out on the test bench to investigate the incorrect use, it was found that at temperatures above 800 °C in ceramic discs, the materials used for the clutch components must be selected with a special correspondence.
The maximum thermal load for discs made of fiber-reinforced SiC is 1400 degrees Celsius and is not a critical factor.
Discs containing titanium lined with riveted sinter liners 9 were chosen for car discs. This choice is a combination of resistance to centrifugal forces and high temperatures along with low weight and reduction of the rotating part (Figure 5).

Figure 5: The small diameter of the clutch discs creates a lower position for the crankshaft
Comprehensive tests and extensive tests in the vehicle, under heavy loads, showed that ceramic composite clutches can compete with today’s conventional clutches, at least in terms of service life.
Engineers have come up with more requirements for the Carrera GT clutch. Although the overall cost is higher than that of conventional clutches due to the more complex manufacturing process and lower product quantity, the ceramic composite clutch is pioneering a line of development that holds a very promising future for high-stress applications in standard production vehicles.
The comprehensive experience that Porsche engineers have gained in the fields of ceramic composites, ceramic composite clutches and production series can be used in the development of various types of vehicles, especially in the high engine rev range.
Table 1: Technical information of manufactured clutch
pic
Car chassis
Porsche Carrera GT is a high-tech product. In the development process, Porsche engineers integrated pure racing technology into a high-performance vehicle for everyday use.
As it is customary in the racing engine, Carrera GT uses the characteristic of climbing chassis (Figure 6).
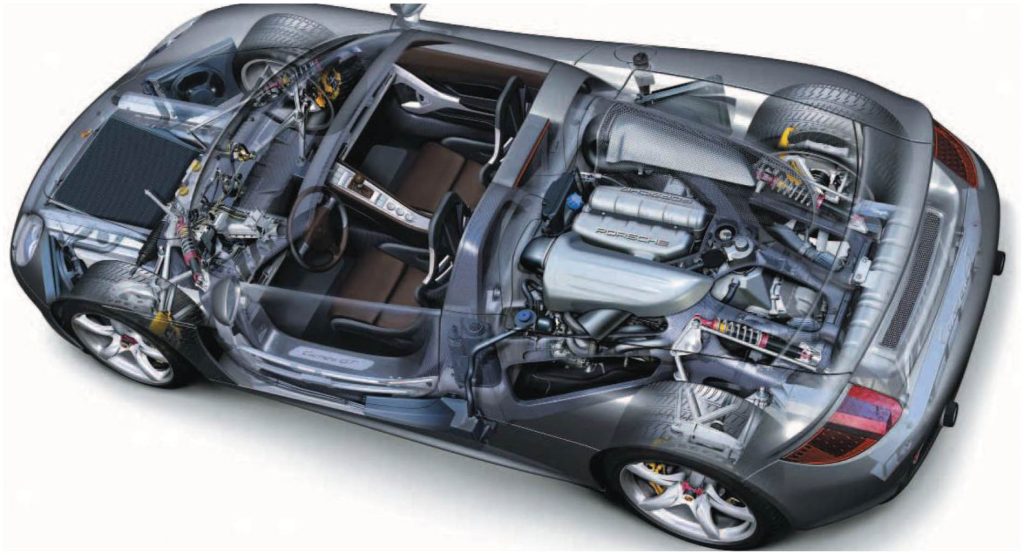
Figure 6: Carrera GT like a real racing vehicle, chassis 11 feature has it. So that the moving part, chassis, underframe 12, engine and crash structure are completely connected with each other.
Low weight, maximum torsional stiffness and low center of gravity have been the goals of Porsche development engineers.
As is typical with a racing engine, the chassis is the centerpiece of the Carrera GT, which includes the 13-piece body, windshield frame and rollover structure.
The body should be made of carbon fiber reinforced plastic (14 CFRP), as the only fiber reinforced composite that guarantees properties such as light weight, maximum stiffness, optimal performance, mobility and safety.
The body performs all the tasks such as the transmission of reaction forces from the chassis and the movement characteristics that are normally performed by the body shell.
Unlike the usual body design that has a large number of individual parts, the integrated body is produced from a number of carbon fiber reinforced plastic shells that are glued together under high pressure in furnaces.
This solution presents another difficulty, what will the rear of the car look like and what is the best way to connect it to the integrated body (Figure 7).
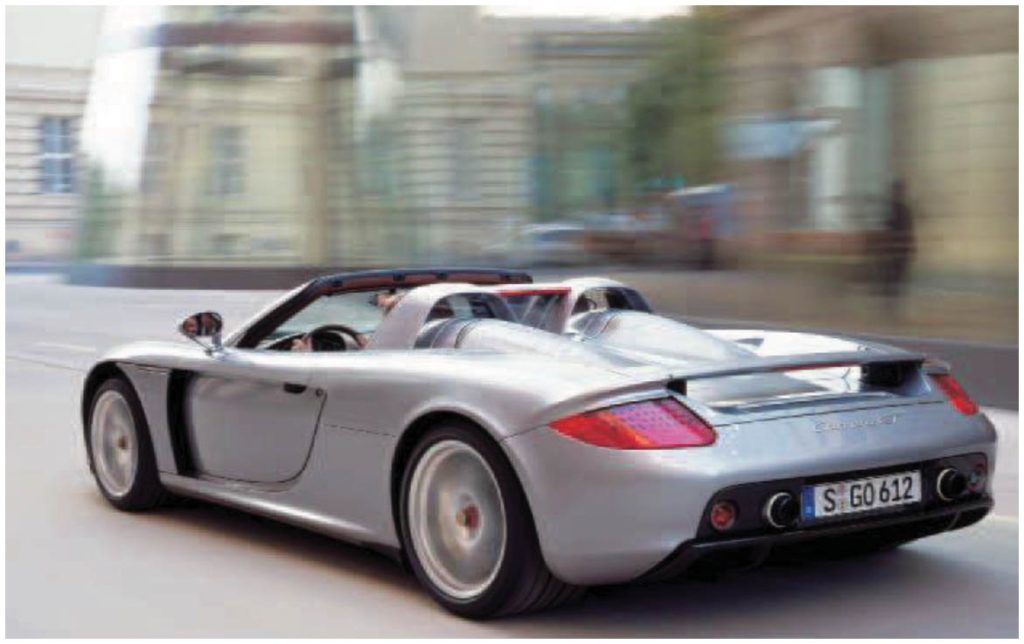
Figure 7: Rear view of Porsche
When this car is used, underbody 15 It is constantly exposed to extreme sources of stress, heat, oil, moisture or road salt.
Extensive tests and theoretical analyzes convinced Porsche engineers that the rear of the car could be produced from carbon fiber reinforced plastic.
This result created a revolution in the field of car manufacturing. Because previously, these materials were used only in aerospace applications or for panels and structural components of racing cars.
The chassis and bolted underbody are the main structural components that form a rigid torsional and helical unit 16 as the backbone of Carrara JT.
They help to suspend the front and rear wheels and absorb the forces caused by the impact of the vehicle. At the same time, they play a supporting role as a bearing for the panel and internal components.
A unibody body frame is the standard in car construction these days, but the Porsche Carrera GT has a rotating chassis like a true racing car.
Rotating chassis, a set including chassis, underbody, driver, movable device 17 And it is the main body.
Structural components are made by a manual process known as sandwich design. The integrated body consists of about 1000 individual blanks.
The production process for the CFRP component with the placement of mats 18 Carbon fiber impregnated with synthetic resin begins in the corresponding production molds.
The type of resin, the type of fibers, the orientation of the fibers and the thickness of the fabric mats depend on the load range or the area of application and the subsequent performance of the relevant part. Therefore, these parameters should be defined.
Porsche has obtained the necessary information regarding the behavior of the structure under operating loads and with regard to safety requirements at the global level using comprehensive FEM simulations.
Depending on the need, additional layers of 20 mm thickness are placed on the mats in a honeycomb pattern with the help of adhesive films that cause compression between the outer layers of carbon fiber reinforced plastic.
Honeycomb material, depending on the function of the desired part, aluminum or aramid paper 19 is made (Figure 8).
Then, additional impregnated layers of carbon fiber mat are laminated on it. This work increases the strength of components that are exposed to a high level of stress.
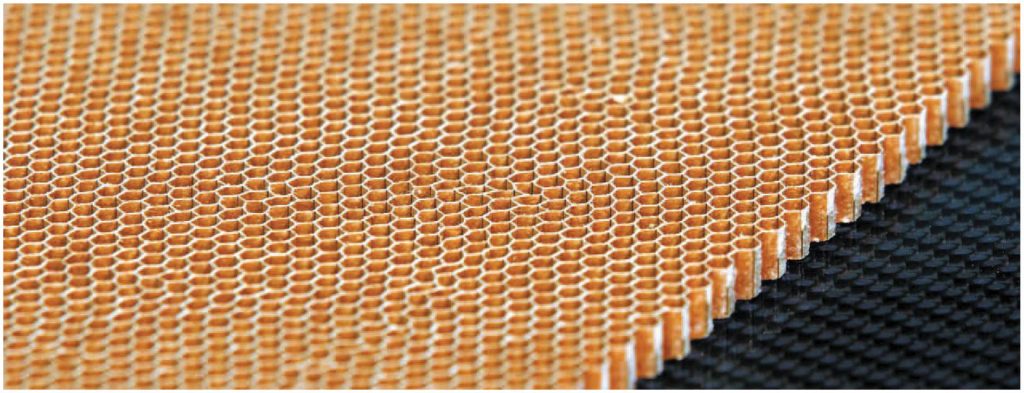
Figure 8: Honeycomb materials are created between individual CFRP layers to improve the strength of parts that are under high stress levels.
Aluminum inserts into the laminate structure are used to attach additional components to the carbon fiber reinforced plastic structure under load, from simple torsional connections to connection points for chassis or powertrains that are subject to high levels of stress, and are structurally compatible with The carbon fiber layers are bonded in an autoclave (Figure 9).
Porsche engineers have conducted detailed research on the special electrochemical properties of carbon fiber materials in conjunction with common metal materials used in automobile production.
Accordingly, they are able to develop coatings or shields 20 They meet high quality requirements based on the type of application.
Finally, the mold under a closed air 21 It is covered with a foil, then drained and placed inside an autoclave at a pressure of 6 to 8 bar and depending on the given conditions at a temperature above 180 degrees Celsius.
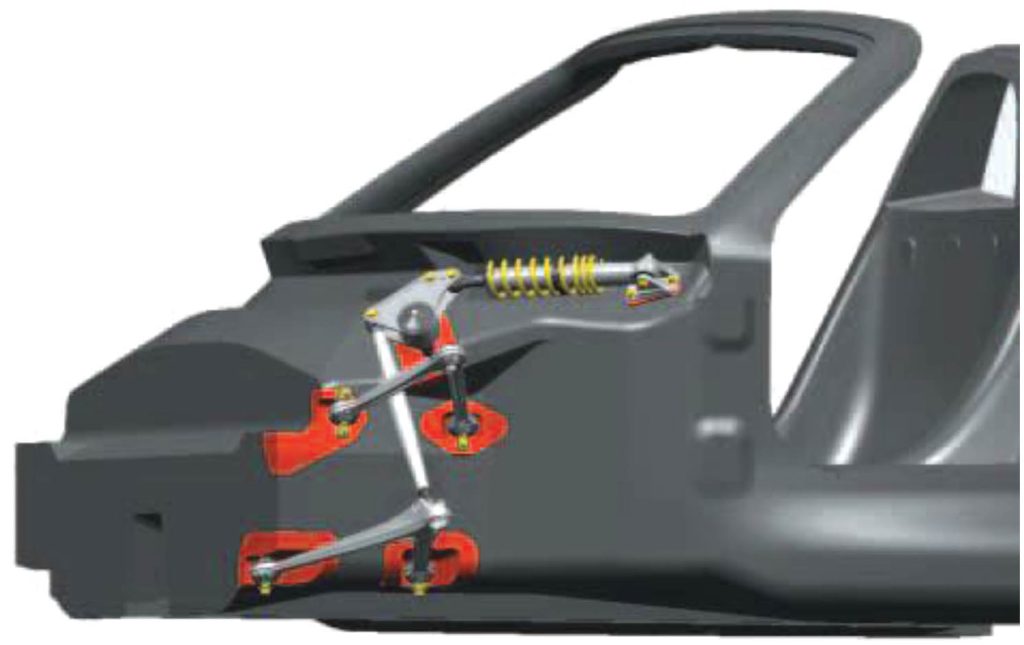
Figure 9: Parts attached to laminates on aluminum inserts
During this process, the resin systems are polymerized and the honeycomb or placements 23 They are connected through adhesive films with carbon fiber.
Despite its remarkable capacity to withstand stress, most carbon fiber reinforced plastic parts weigh 40 percent less than their conventional counterparts, meaning the Porsche Carrera GT sets new weight standards. The whole integrated body weighs 100 kg.
Porsche engineers have chosen carbon fiber composites as the material for the Carrera GT performance parts.
Because only this material is available with the ability to combine maximum performance and driving mobility with minimum weight and maximum strength.
As a result of these properties, high-tech fiber also offers a very high standard of safety. Carrera GT car has reached the highest level of torsional and bending strength in standard car production. This remarkable strength is even higher than the modern coupe model.
The concept of safety in the Porsche Carrera GT is based on the current requirements in racing cars. This is done in order to produce a single body free of any structural damage in the prescribed tests.
A rigid cabin ensures the necessary safe space for the passenger. Most of the applied energy is absorbed by the impact-resistant structure, which is made of austenitic stainless steel (Figures 10 and 11).
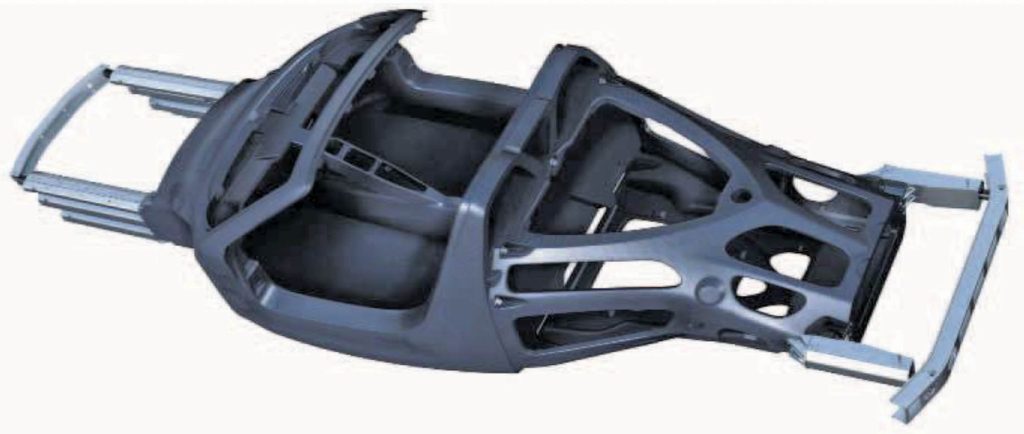
Figure 10: chassis, subframe and impact-resistant structure; Austenitic stainless steel absorbs most of the crash energy
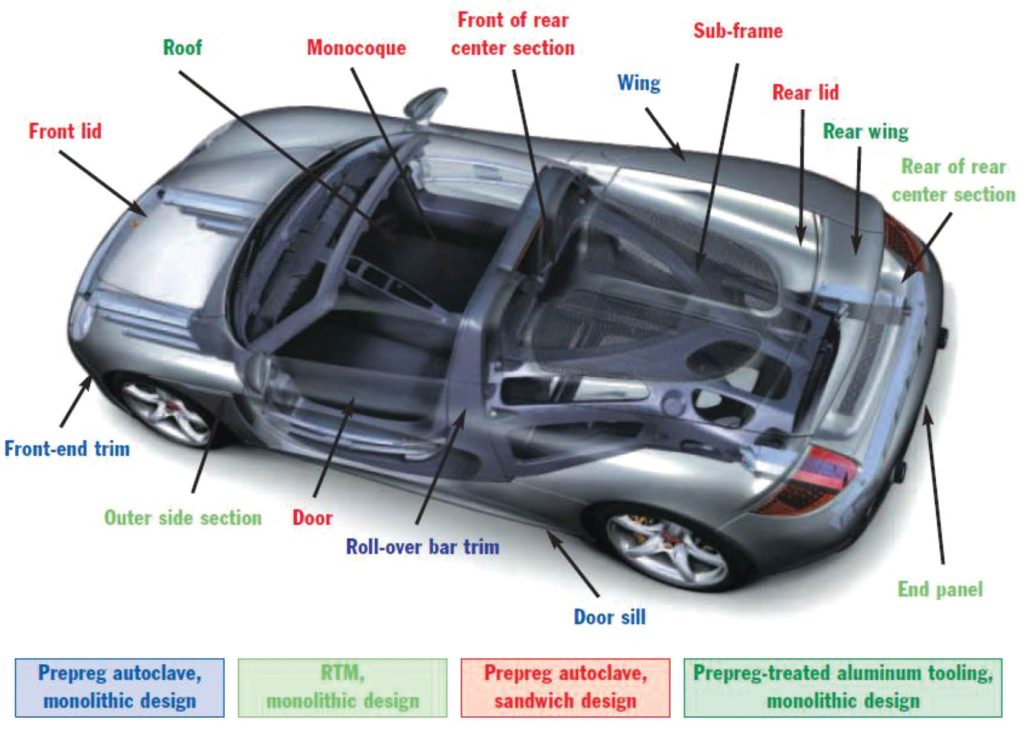
Figure 11: Integrated body and subframe components and a number of other parts produced with CFRP
Porsche has investigated the car’s crash behavior in extensive simulated tests. These engineers conducted extensive research to gain an understanding of the overall system.
In this context, appropriate simulation tools were defined and the material structure was drawn in detail in an FE model.
The material laws are extracted and the simulations and experiments are systematically compared with the key stages of the development process.
In order to investigate the reaction of integrated and sandwich materials in combination with metallic materials, for example, each individual carbon fiber layer is drawn in a computational model.
Engineers have extensively optimized this method in which the behavior of carbon fiber and steel in a crash can be calculated with a very good degree of correlation with experimental research.
Following the development of the Porsche Carrera GT, the company has deeply investigated carbon fiber reinforced plastic and its properties under the most varied conditions.
Aspects such as long-term and corrosion behavior, surface quality and fracture properties have been investigated, calculated and optimized in detail for the Porsche Carrera GT.
Also, Porsche has managed the development of carbon fiber reinforced plastic components for the interior and exterior in the highest quality with regard to appearance.
The extensive knowledge of the various use cases for fiber composites in the Carrera GT has provided Porsche engineers with conditions that enable them to propose suitable solutions in all cases related to carbon fiber reinforced plastic.
This experience has provided Porsche engineers with the ability to develop carbon fiber parts even outside the automotive field.
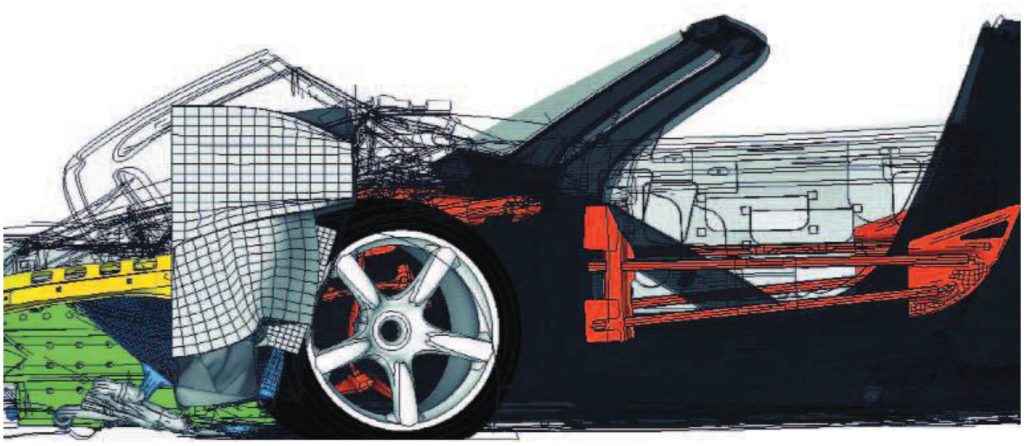
Figure 12: Calculation of the accident simulation from the front -40% overlap corresponding to the experimental test
Conclusion
Ceramic matrix composites are a subgroup of composite materials as well as technical ceramics that include fibers embedded in a ceramic matrix.
The growth and development of ceramic composites has been related to solving problems related to conventional technical ceramics such as alumina, silicon carbide, aluminum nitride, silicon nitride or zirconia.
Because these ceramics are easily separated in mechanical and thermomechanical loads due to cracks created by small defects or scrapers.
The comprehensive experience that Porsche engineers have gained in the field of ceramic composites, ceramic composite clutch, carbon fiber reinforced plastic and production series is also used in the development of other cars.
0 Comments