Biopolymers or biodegradable polymers are a group of polymers that are decomposed by the bacterial process and lead to the formation of by-products such as various gases, water, biomass and mineral salts. These polymers are made naturally and synthetically and are mainly composed of ester, amide and ether functional groups. Increasing concerns with the rising price of fossil fuels and its impact on the environment and reducing the amount of greenhouse gas emissions have made it necessary to try to replace conventional petroleum-based plastics with other biopolymers. In this article, ACT Group has investigated the benefits and potential applications of biopolymers in automobile industry.
Introduction
Polymers have become one of the essential parts in the automobile industry due to their ability to replace many heavy metal parts in the interior and exterior of the car.
Today, car interior parts such as dashboard, roof carpet, door cover, gaskets, seat fabric, upholstery, trunk decorations, sound insulation are exclusively made of polymer materials.
As for external parts, the use of polymers is less compared to internal parts, but it is not limited to the bumper shell, but polymers are used in fenders, grille, etc.
In the last decade, the use of biopolymers (bio-based polymers) has been proposed in the automobile industry, which plays a very important role in reducing the use of petroleum products in order to protect the environment.
In addition to being lighter, these biopolymers are very affordable and easy to mold and recycle.
Currently, the use of environmentally friendly materials to produce a variety of products has become a norm, and developed and developing countries have incentive programs to conduct research on biopolymers in automotive applications.
Introduction of biopolymers
Biodegradable polymers, commonly named as biopolymers, are mainly obtained from various natural sources.
Plastics such as polylactic acid (PLA), polycyclic aromatic hydrocarbon (PAH) and starch are the most widely used biopolymers that leave the least footprint of carbon dioxide.
Of course, it should always be noted that biodegradability is a characteristic of polymers and is independent of their origin.
In other words, it is possible to make some petroleum-based polymers degradable by changing the molecular structure.
Therefore, currently, biopolymers mean biopolymers of renewable origin. Because this category is the most abundant and common biopolymers that can be categorized.
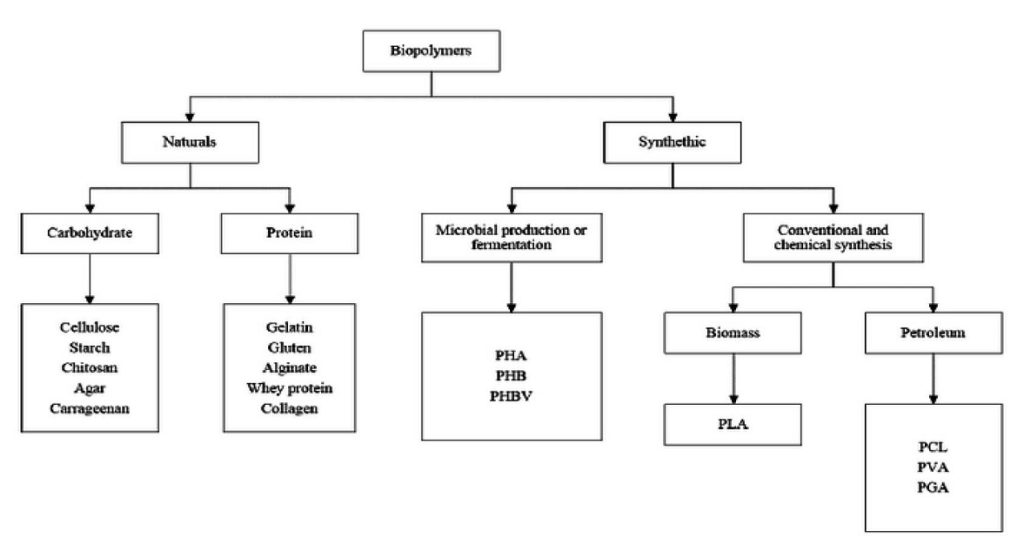
Figure 1: Classification of biopolymers
Classification of biopolymers
In general, biopolymers can be classified according to the origin of their preparation as follows:
Sugar-based biopolymers
The most common and widely used sugar-based biopolymer that has great potential for multiple applications, including the automobile industry, is polylactic acid (PLA).
The primary material of PLA monomer is lactic acid, which is obtained from milk sugar or lactose and is extracted from natural sources such as potatoes, sugarcane and wheat.
Polyhydroxybutyrate (PHB), another type of biopolymer produced by microorganisms and used as an energy storage molecule.
Starch-based biopolymers
Starch is a biopolymer and a form of carbohydrates that is widely found only in plants and is stored in their tissues.
However, the main component of starch is glucose, and it can be converted to glucose using temperature or other chemical stimuli.
Plants such as potato, corn and wheat are the main sources of starch.
Cellulose-based biopolymers
Cellulose is the most abundant biopolymer found in plant cell walls. The main ingredient of cellulose is glucose.
Cellulose can be widely used as a filler or softener in other biopolymers to improve properties.
Biopolymers based on synthetic materials (Synthetic biopolymers)
Synthetic polymers such as aromatic and aliphatic polyesters are produced on the basis of oil and during chemical reactions.
Like biopolymers of natural origin, biopolymers of synthetic origin also have the ability to be composted, which include:
Poly (caprolactone) (PCL), Polyglycolic acid (PGA) and Polyhydroxybutyrate (PHB), which are all three aliphatic polyesters and polybutylene adipate-co-Terephthalate (PBAT) is an aromatic copolymer that is chemically synthesized from petroleum-based raw materials.
The use of biopolymers in automobile industry
The use of biopolymers in automobile industry in the manufacture of body parts effectively improves fuel efficiency and brings design diversity, passenger comfort and insulation properties.
In addition, it not only reduces dependence on fossil fuels, but also helps curb the carbon footprint on nature.
However, mechanical properties such as thermal properties of biopolymers are not enough to compete in the automotive sector compared to conventional polymers.
These biopolymers are biodegradable or compostable, but they do not show the mechanical properties required in automotive engineering applications.
However, the combination of these biopolymers is suitable for applications such as car interior parts.
Automotive industries are willing to use biopolymers as car body components. PLA and PBS are two biopolymers that have received special attention from the automobile industry, which is due to the nature of biodegradability and its properties, which are close to the quality standards required by the industry.
Automotive interior components such as seat upholstery, foam, body lining and woven and non-woven textiles are some of the applications that have the potential to use biodegradable polymers such as PLA.
Load bearing, strength, low degradation against sunlight, wear resistance and high durability are some of the important criteria of polymer materials in automotive applications.
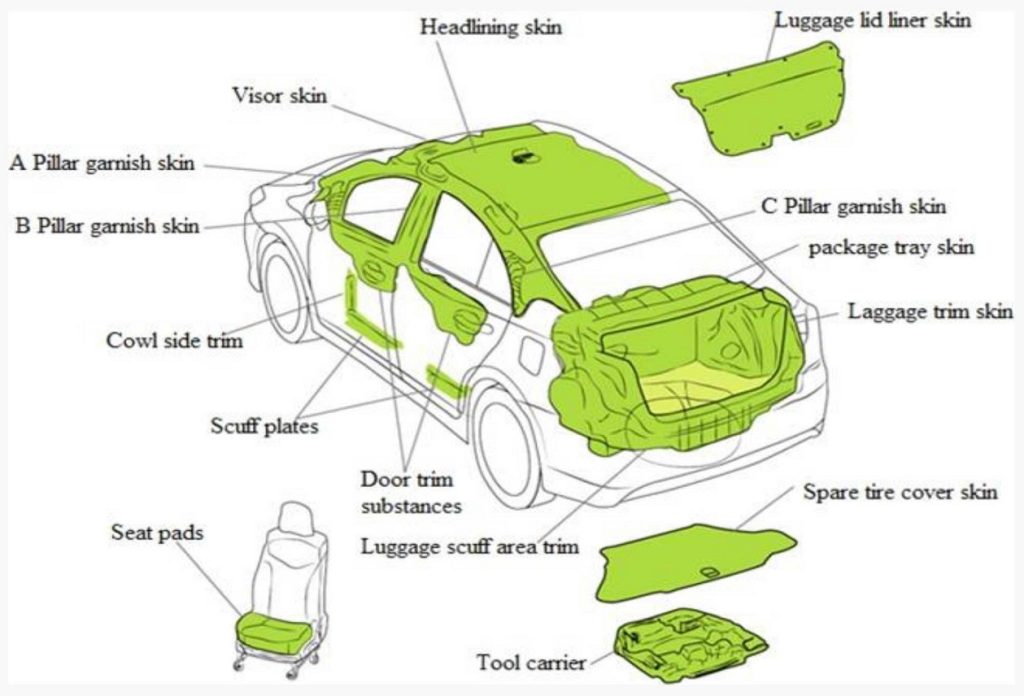
Figure 2: The use of biopolymers in various car components
Apparently, a revolutionary change in the use of biodegradable polymers in the automotive sector seems to be taking place.
Japanese companies such as Mazda and Mitsubishi were pioneers in this field, and Ford Motors also emphasized that they use biopolymers for internal car parts in their production.
Therefore, biopolymers obtained from renewable sources have been considered by Ford Motors for use in the interior of customized cars instead of using petroleum-based polymers.
Bio fabrics are used as seat covers and interior door decorations in cars. Among all existing biopolymers, PLA is always considered as an important and key biopolymer due to its high strength, ease of processability, biocompatibility, and biodegradability, and ease of molding in complex shapes and sizes.
Mitsubishi Chemical Co., Ltd. jointly established a company and succeeded in developing heat-resistant biodegradable PBS product in 2016.
This bio -PBS is compatible with fibers and increases mechanical properties, strength and stiffness.
Recently, in 2018, Ornl National Laboratory researchers developed a semi-biopolymer that is able to replace the styrene part in Styrene/ABS elastomer thermoplastic, which is named Lignin.
This ABS/Lignin bio-composite is three times harder than pure ABS and can be recycled up to three times.

Figure 3: The use of biopolymers in car body
The first use of biopolymers in automobile industry dates back to the 1930s, but the last 15 years have seen a significant expansion of their use in automotive applications.
Japanese automakers seem to be leading the way in using bioplastics in their cars. But in the end, American Henry Ford was the pioneer.
The use of bio-based polymers in automobile companies:
Ford
Henry Ford founded the Ford Motor Company and developed the company’s first mass production assembly line.
He established a link between agriculture and industry and pioneered the use of bioplastics in the automotive industry in Iran.
In the 1930s, the company used soy bioplastics to reduce car weight and increase mileage efficiency, and made some Ford car parts from soy bioplastics.
In 2000, it started using and testing polymers made from renewable fibers, and in 2003, it used PLA fibers in the roof and floor carpets of its U model cars, and finally in 2018, it started testing on plastics made from fibers. Based on wheat straw, coconut and guava plant.

Figure 4: Internal waste bin based on PP reinforced with 20% bio fibers based on wheat straw
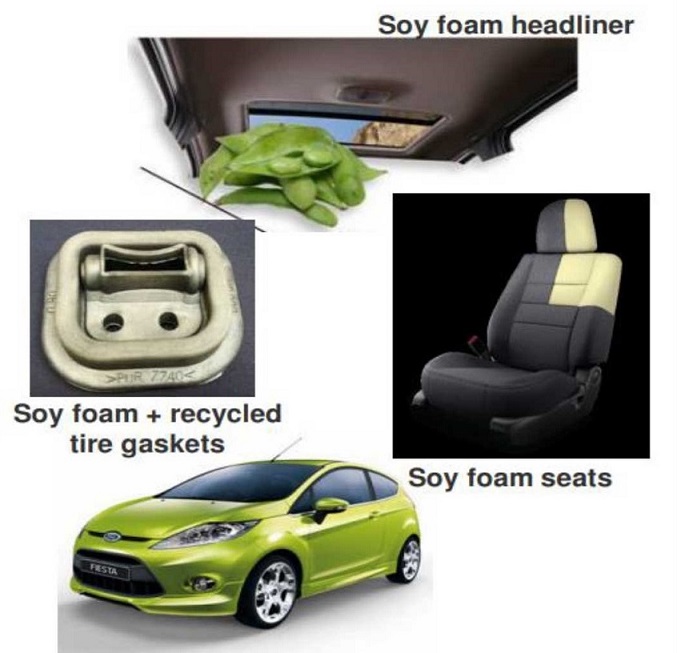
Figure 5: Parts made of soy-based polyurethane foam
General Motors (General Motors-GM)
General Motors uses wood based on Bio-PP for the seat backs of the Cadillac de Ville and Bio-PP based on linen for decorative parts and pillar frames in the Chevrolet Impala.
Chrysler was the first car manufacturer to make economy cars based on composites.
Used a Bio-Based that contained kenaf, hemp and polypropylene for interior door panels in Chrysler Sebring cars.
Mazda
Mazda began developing bioplastics under the brand name Mazda Biotech Materials, and in 2006 developed the first mass-produced PLA under the brand name Biofront™.
This PLA is used in car seat fabric as well as for floor mats, pillar covers, door trim, front panel and roof materials.
Mazda claims to be the first company to achieve over 80% plant-based content for interior fittings (in hybrid and hydrogen vehicles) and 100% plant-based bio-fabric for seat covers.
Toyota
Toyota has used Bio-Based Polyesters, Bio-PET and PLA. They claim to be the first to use Sugarcane-Based PET in vehicle linings and other interior surfaces.
Toyota SAI and Toyota Prius were the first models to use a number of bioplastics in applications such as headliners, sun visors, and floor mats.
During 2015, Toyota used PLA-PET blends to produce foam rubber parts and interior trim parts, and PLA-PP alloy.
Used to produce injection molding parts and interior decorations. Many Toyota vehicles now have Soy-Based seat cushions, including the Prius, Corolla, Matrix, RAV4, and Lexus RX350.
Also, Toyota has used biopolymer containing 20-37% starch to produce air vents in Toyota Prius Alpha.
Mitsubishi
Mitsubishi Chemical has developed a bioplastic called BioMat that can be Mass-Produced for automotive interior parts such as door panels, trim and trim, structural instrument panels, console lids, air ducts and doors.
BioMat is based on biosuccinic acid prepared from Bio-PBS.
Fiat
Fiat and DuPont received the Society of Plastics Engineers Automotive Innovation Award in the environmental category for using castor Oil-Based polyamide in some fuel lines.
This Polyamide is a long chain of nylon products with a renewable source that contains between 60 and 100 percent Bio-Based materials.
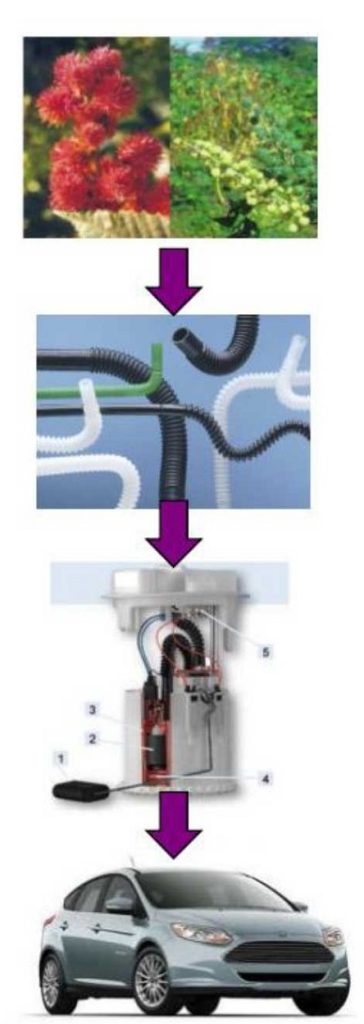
Figure 6: Bio-Based Polyamide derived from castor oil in automotive fuel pipes
In fact, Fiat used Polyamides derived from castor oil and Polyurethanes derived from soybeans in more than one million cars.
Fiat cars ordered from Brazil contained Polyurethane seat foams with 5% soy Polyol.
Lexus
The Lexus CT200h featured Bio-PE made from bamboo and corn in its trunk, speakers and floor mats.
Lexus HS250 has bio parts in trunk decoration, side cover, seat cushion, door scratch plate and tool box.
Mercedes Benz
Daimler company uses hemp, linen and sisal fibers in plastics for door linings. The Mercedes-Benz concept car is also a vehicle made in a laboratory from organic Bio-Fibers.
This car can be made of stronger steel, lighter than metal, and compostable at the end of its life.
Other Mercedes Benz models have Bio-PE with linen in the Engine, Gearbox Cover and in the panels under the body. Mercedes-Benz Beauty Cover is made of 70% bio Polyamide (PA 4,10).
BMW
BMW has used Wood-Based bio composites produced by Johnson Controls for its panels, making them 20 percent lighter than traditional materials.
Some BMW series contained up to 24 kg of linen and sisal.
References
- Y. Murtaja, L. Lapčík, B. Lapčíková, S. Gautam, M. Vašina, L. Spanhel, J. Vlček, Intelligent High-Tech coating of natural biopolymer layers, Advances in Colloid and Interface Science, 304, 2022, 102681.
- S. Sharma, B. Sharma, A. Manral, PK Bajpai, P. Jain, Chapter 11- Biopolymers in the automobile and adhesive industries, Elsevier, 2021, 261-280.
- GP Udayakumar, S.Muthusamy, B.Selvaganesh, N.Sivarajasekar, K.Rambabu, S.Sivamani, N.Sivakumar, JP Maran, AH-Bandegharaei, Ecofriendly biopolymers and composites: Preparation and their applications in water-treatment, Biotechnology Advances, 52, 2021, 107815.
- D. Verma, V.Dogra, AK Chaudhary, R.Mordia, Advanced biopolymer-based composites: construction and structural applications, Woodhead Publishing, 2022, 113-128.
- A.George, MR Sanjay, R.Srisuk, J.Parameswaranpillai, S.Siengchin, A comprehensive review on chemical properties and applications of biopolymers and their composites, International Journal of Biological Macromolecules, 154, 2020, 329-338.
- A.Vinod, MR Sanjay, S.Suchart, P.Jyotishkumar, Renewable and sustainable biobased materials: An assessment on biofibers, biofilms, biopolymers and biocomposites, Journal of Cleaner Production, 258, 2020, 120978.
- RA Pradhan, SS Rahman, A.Qureshi, A.Ullah, Chapter 12- Biopolymers: opportunities and challenges for 3D printing, Biopolymers and their Industrial Applications, Elsevier, 2021, 281-303.
- A.Tariq, SA Bhawani, KM Alotaibi, A.Moheman, Chapter Six-Smart biopolymers and their applications, Woodhead Publishing, 2021, 145-167.
- B. Sharma, P.Malik, P.Jain, Biopolymer reinforced nanocomposites: A comprehensive review, Materials Today Communications, 16, 2018, 353-363.
- AA Mohan, AR Antony, K.Greeshma, JH Yun, R.Ramanan, HS Kim, Algal biopolymers as sustainable resources for a net-zero carbon bioeconomy, Bioresource Technology, 344, Part B, 2022, 126397.
- GA Lutzu, A.Ciurli, C.Chiellini, FD Caprio, A.Concas, NT Dunford, Latest developments in wastewater treatment and biopolymer production by microalgae, Journal of Environmental Chemical Engineering, 9, Issue 1, 2021, 104926.
- WPSL Wijesinghe, MMMGPG Mantilaka, KAA Ruparathna, RBSD Rajapakshe, SAL Sameera, MGGSN Thilakarathna, Filler matrix interfaces of inorganic/biopolymer composites and their applications, Woodhead Publishing, 2020, 95-112.
- A.Muhammad, MdR Rahman, R.Baini, MKB Bakri, Applications of sustainable polymer composites in automobile and aerospace industry, Advances in Sustainable Polymer Composites, Woodhead Publishing, 2021, 185-207.
- M.Nasrollahzadeh, N.Shafiei, Z.Nezafat, Application of biopolymers in bioplastics, Biopolymer-Based Metal Nanoparticle Chemistry for Sustainable Applications, Elsevier, 2021, 1-44.
- HT Sreenivas, N.Krishnamurthy, GR Arpitha, A comprehensive review on light weight kenaf fiber for automobiles, International Journal of Lightweight Materials and Manufacture, 3, 2020, 328-337.
0 Comments